Transport Ladle in Stainless Steel Production
In transport ladles for stainless steel production, concepts based on magnesia-alumina-carbon bricks are increasingly used and, depending on the slag chemistry, can lead to significantly higher ladle lining life than dolomite-carbon-based concepts.
Mayerton produces a wide range of high-quality MAC products that are already used by many customers and have significantly improved the price/performance ratio compared to traditional Doloma linings.
Impact Area
During tapping, the zone in which the steel stream from the converter hits the ladle bottom or the ladle side wall is subject to special thermomechanical requirements.
AMC bricks can withstand these conditions exceptionally well since their mineralogical composition causes them to form spinel when used in the ladle. Spinel is a very tough and hard mineral and thus improves resistance to mechanical impact. In addition, the spinel formation reaction is a space-demanding process, so it is associated with increased volume, further densifying and mechanically strengthening the bricks.
Mayerton offers specially developed brick grades with balanced alumina-magnesia-carbon ratios specifically for this lining area, which can withstand the mechanical challenges and thus contribute to better overall lining durability.
Safety Lining
Mayerton generally recommends brick linings as safety linings, preferably made of fired magnesia or magnesia-chromite bricks.
In the bath area, materials based on non-basic raw materials, such as bauxite or mullite, are used as well. In any case, shapes should be used that guarantee high mechanical stability.
For this purpose, Mayerton offers different tongue and groove brick designs that can withstand the breaking out of worn working linings without damage and can be used for several ladle campaigns.
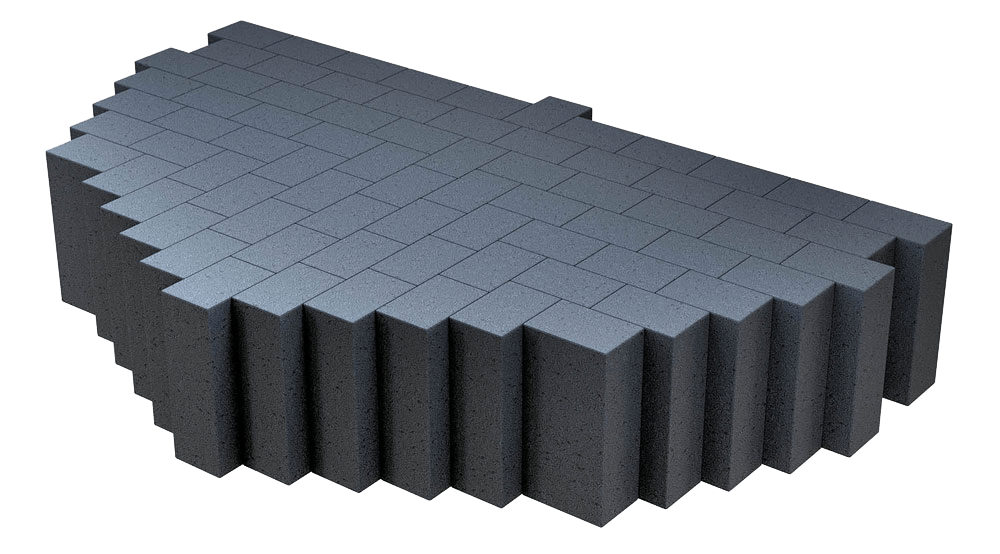