Applications: RH Degasser
The RH degasser (Ruhrstahl Heraeus process) is used in the production of high-quality steels in secondary metallurgy for degassing the melt.
The RH plant can also be equipped with an oxygen lance (RH-OB) and is therefore ideally suited for the production of deep decarburized and inclusion-free steels (ULC and IF grades).
To degas the melt, the RH degasser is immersed in the liquid steel in the treatment ladle and a partial quantity is sucked into the reaction vessel under vacuum.
To start the treatment 2 immersion tubes, the so-called snorkels, dip into the molten steel, whereupon the vessel is evacuated. Argon or nitrogen is introduced into the inlet snorkel to support the upward movement of the liquid steel. In the vacuum vessel, the molten steel is degassed and decarburized and flows back into the ladle through the outlet snorkel.
The aim of the treatment is to degas the melt, especially to remove hydrogen, in order to reduce the brittleness of the finished steel. RH plants are preferably used in the production of high-quality flat steels.
Alloy chutes and burner blocks are assembled and drilled in the factory and can be delivered to our customers either disassembled or fully assembled.
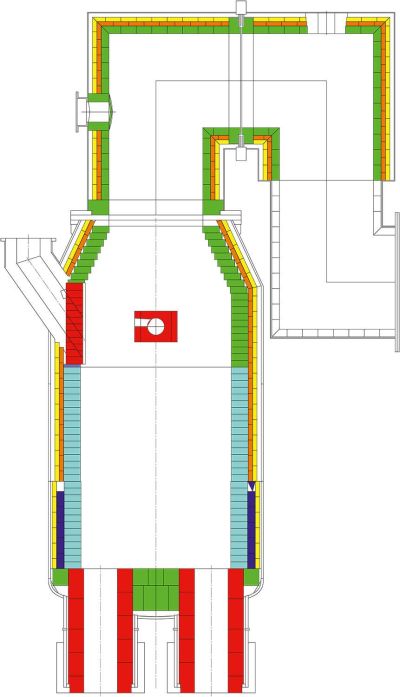
Lining Wear & Material Choice
Fired magnesia chromite bricks are used due to their ability to withstand the highly abrasive conditions of the circulating steel.
Different degasser components subjected to different levels of stress, which can be optimised to operate as economically as possible. In most cases, the snorkels and legs, the lower vessel, the alloy chute and the burner block are subjected to the highest stress and are lined with correspondingly high-quality materials.
Depending on the raw materials used or their combination, a distinction is made between silicate-bonded, directly bonded, and so-called semi-rebonded and rebonded magnesia chromite bricks. Depending on the place of installation and operating conditions, the proportions of magnesia and chromite in silicate-bonded and directly bonded brick materials can vary. In semi-rebonded and rebonded magnesia chromite bricks, fused magnesia chromite is used, which has significantly higher slag and abrasion resistance than pure magnesia.
All our magnesia chromite products are available both without and with salt impregnation to increase hydration resistance.
Mayerton supplies various fired magnesia chromite products, such as highest-grade magnesia, chrome ore and pre-reacted fused magnesia chromite. Depending on the choice of raw materials, the materials are fired at different, but always very high, temperatures in order to make them as resistant as possible to abrasion. The raw materials used, and their precisely coordinated grain curves ensure that the thermal shock resistance is very high despite high erosion resistance and discontinuous wear due to spalling is kept at bay.
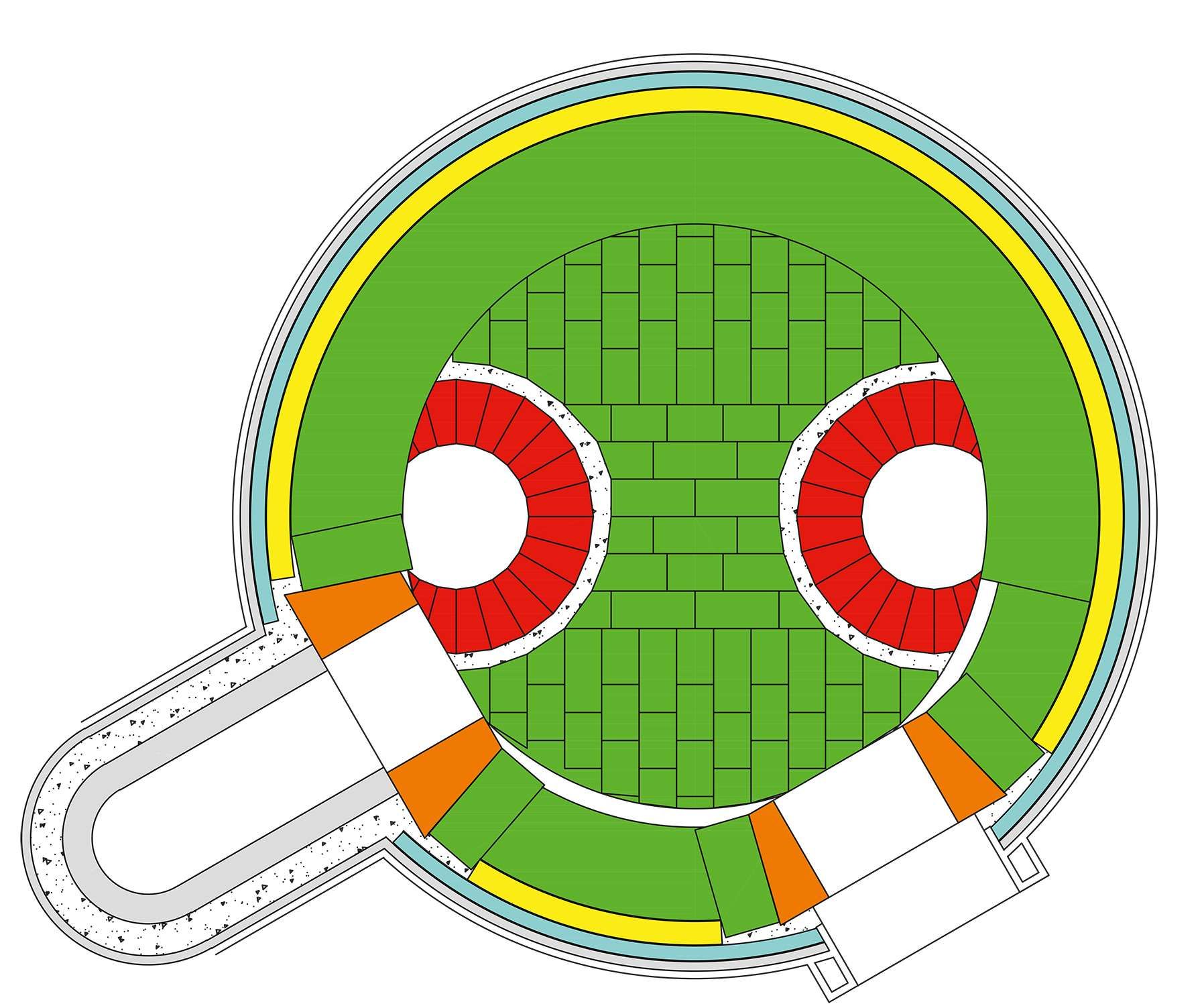
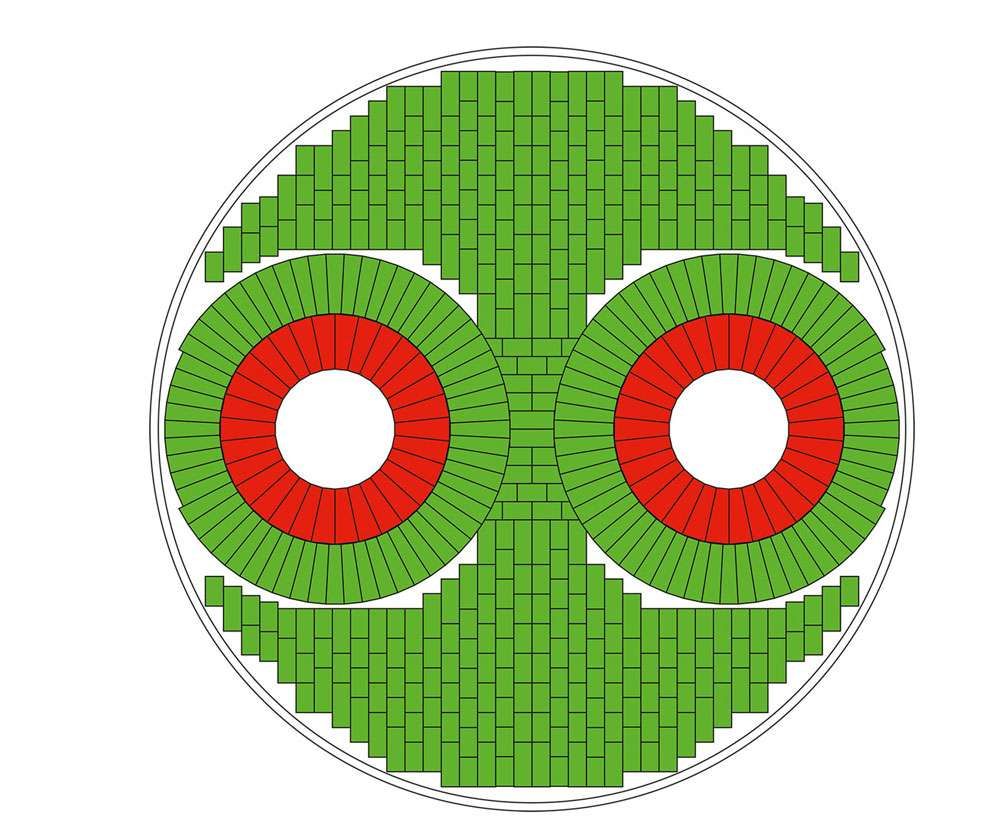
View of different lower vessle bottoms from the upper vessle including Alloy chute and burner block (left) and lower vessle (right).
RH Snorkels
We supply both ready-for-use prefabricated snorkels, as well as (cut-to-measure) bricks for self-assembly.
In addition to planning the brick installation, our designers also carry out the corresponding steel construction planning. Our steel construction partner carries out the steel construction in compliance with all customer specifications.
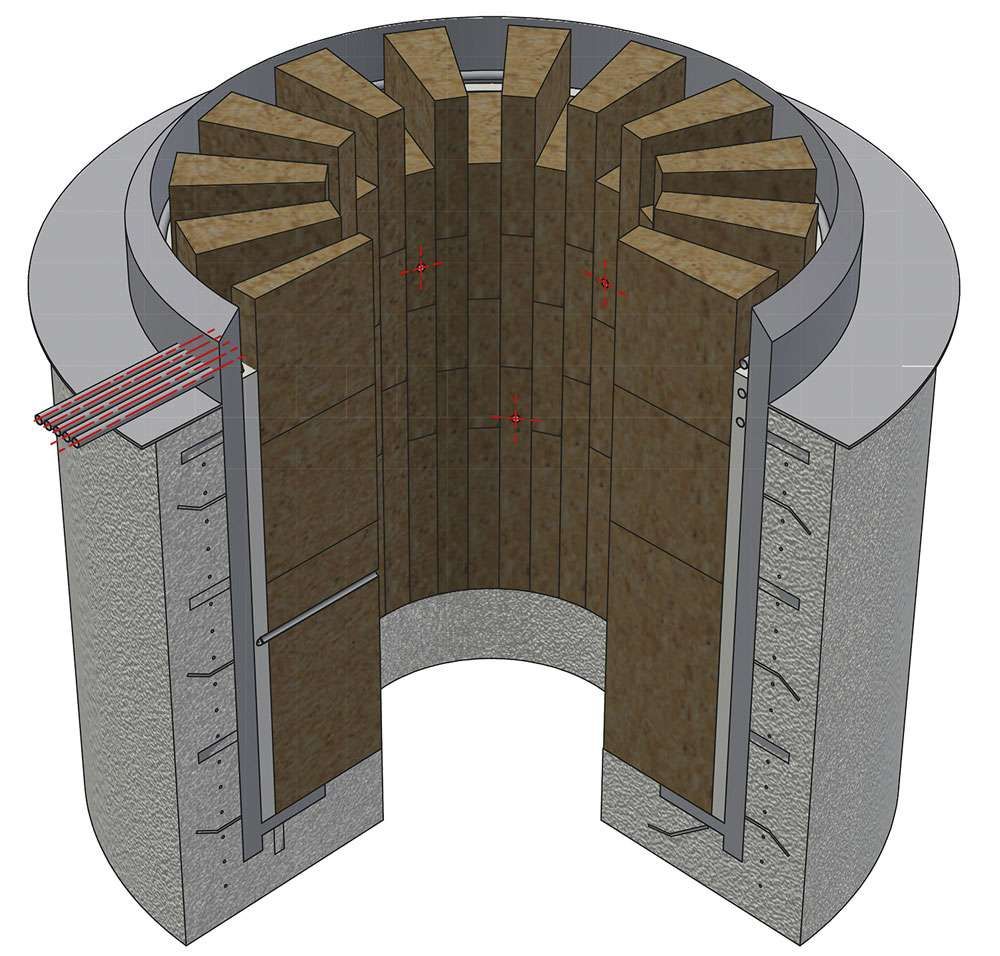
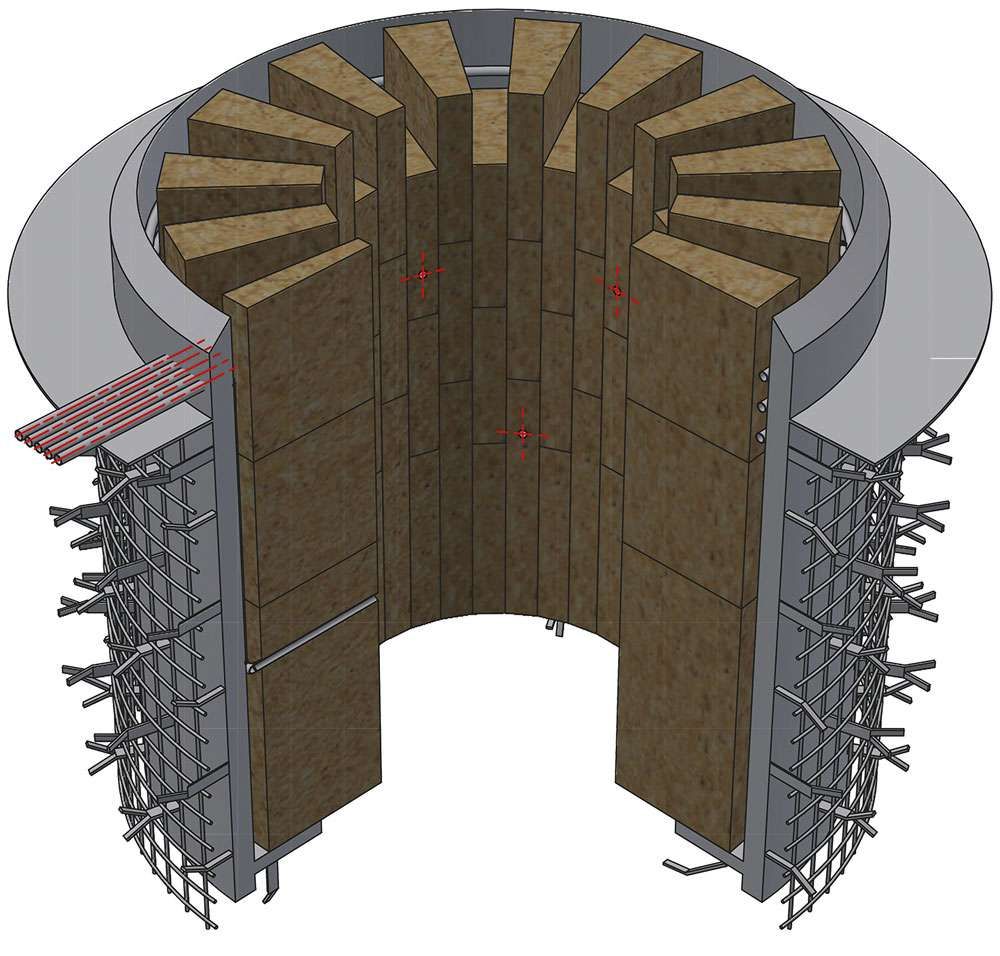
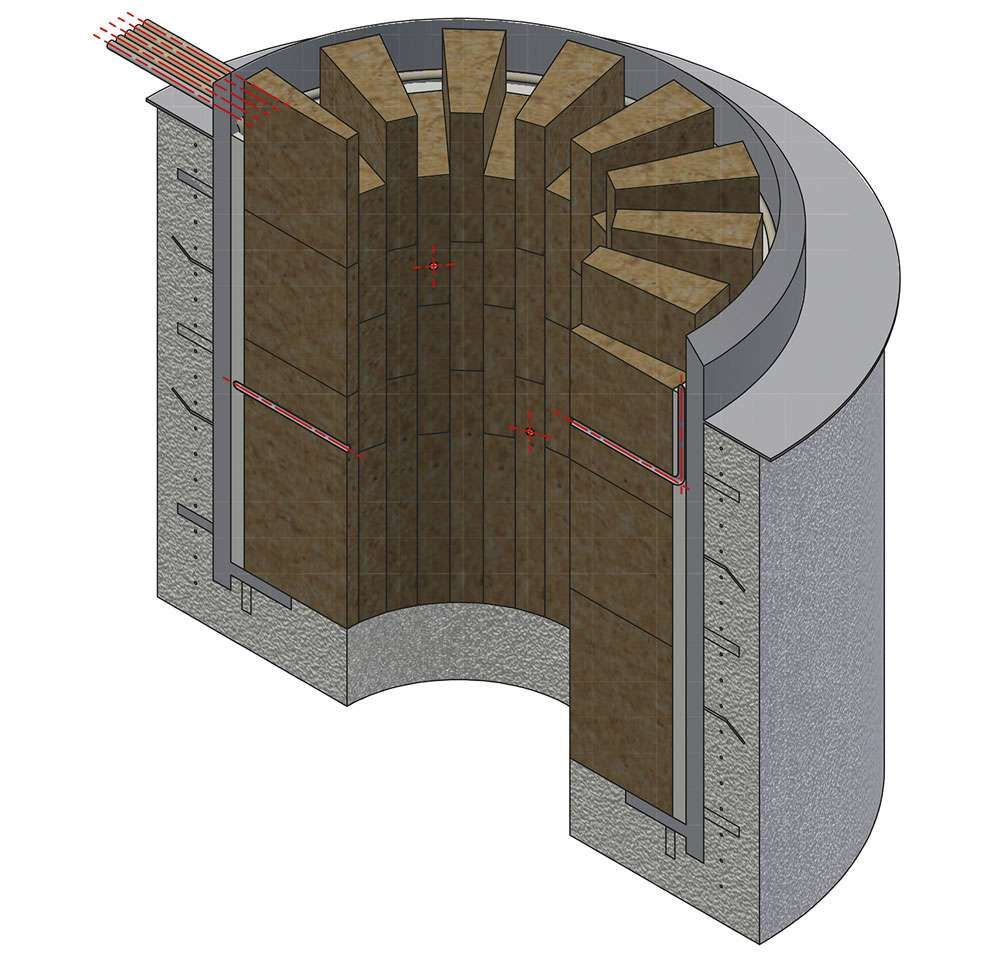